Injection Moulding Manufacturing: The Backbone of Modern Production
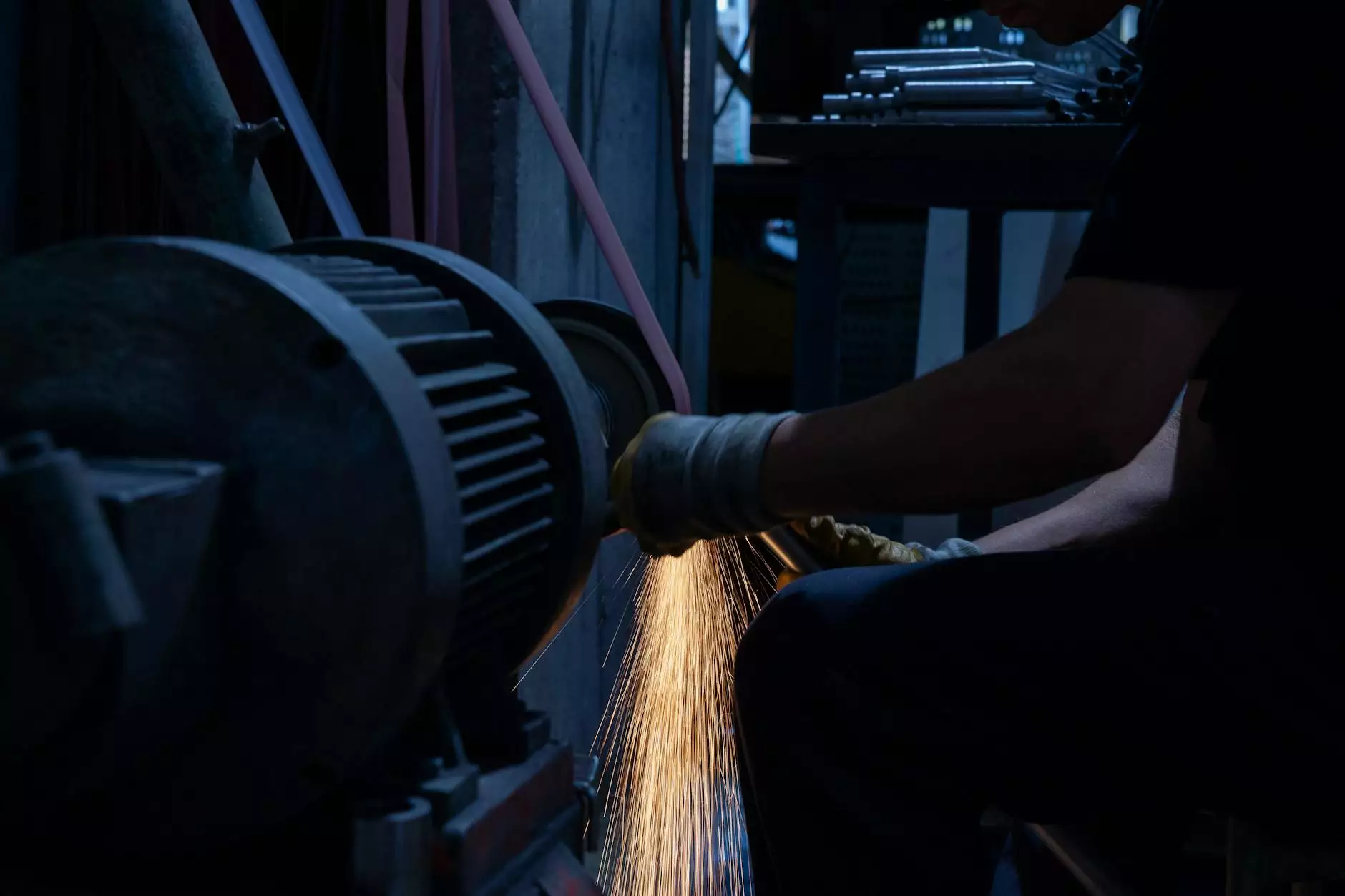
Injection moulding manufacturing is a revolutionary process that has transformed the manufacturing landscape across a multitude of industries. It is a method that allows for the efficient production of complex parts with precision and speed, making it indispensable for sectors ranging from automotive to consumer goods. In this article, we will explore the fundamentals of injection moulding, its advantages, applications, innovations, and why selecting the right partner in this field is crucial for business success.
Understanding Injection Moulding Manufacturing
At its core, injection moulding manufacturing involves injecting molten material into a mould to create precise shapes. This process can utilize a variety of materials including plastics, metals, glass, and ceramics. The method is especially popular for producing plastic items, which can be manufactured rapidly with minimal waste.
The Process of Injection Moulding
The injection moulding process consists of several key stages:
- Material Preparation: Raw materials, typically in the form of granules, are fed into a hopper where they are heated to a molten state.
- Injection: The molten material is then injected into a pre-designed mould cavity under high pressure, ensuring every detail of the mould is filled.
- Cooling: Once the material fills the mould, it is cooled to solidify and take the shape of the mould.
- Demoulding: After cooling, the mould opens to eject the finished product.
- Finishing: Additional processes may include trimming, surface finishing, or assembly of multiple parts.
Advantages of Injection Moulding Manufacturing
One of the primary reasons behind the popularity of injection moulding is the myriad of advantages it offers:
- High Efficiency: The speed at which parts can be produced is unparalleled, allowing for high-volume production runs.
- Cost-Effectiveness: Although the initial setup costs for mould creation can be high, the low cost per unit in mass production significantly offsets this expense.
- Precise Detail: Moulds can be engineered to include intricate designs, which can be replicated with exactness, ensuring consistent quality.
- Material Versatility: A diverse range of materials can be used, offering flexibility in product design and usage.
- Waste Reduction: The closed-loop system of injection moulding minimizes waste, making it an environmentally friendly option.
Applications of Injection Moulding Manufacturing
The applications of injection moulding manufacturing are vast. Here are some prominent industries that benefit greatly from this advanced technology:
1. Automotive Industry
In the automotive sector, injection moulding is extensively used to create components such as dashboards, handles, and exterior trims. The integration of lightweight yet strong plastics helps in improving fuel efficiency and reducing overall vehicle weight.
2. Electronics
From mobile phones to complex machinery, the electronics industry relies on injection moulded parts for enclosures, connectors, and components that require high precision.
3. Consumer Goods
Household items, toys, and packaging materials are often manufactured using injection moulding, showcasing its ability to produce high volumes of basic items efficiently.
4. Medical Devices
The medical industry benefits from the hygienic and precise nature of injection moulding, producing components for devices such as syringes, surgical tools, and diagnostic equipment.
Technological Innovations in Injection Moulding
With the advancement of technology, injection moulding manufacturing has seen numerous innovations that enhance efficiency, precision, and scope. Some notable advancements include:
1. Computer-Aided Design (CAD)
CAD software allows designers to create intricate mould designs on a computer, streamlining the product development phase and minimizing errors before the production stage.
2. 3D Printing for Prototyping
Before committing to a full production run, companies are now utilizing 3D printing to create prototypes. This method reduces development time and costs while allowing for thorough testing of the design.
3. Smart Moulding Technology
Integration of IoT (Internet of Things) technology into injection moulding machinery enables real-time monitoring, predictive maintenance, and enhanced control over the production process.
Choosing the Right Injection Moulding Manufacturing Partner
When engaging in injection moulding manufacturing, selecting the right partner is crucial for the success of your project. Here are several factors to consider:
- Experience: A partner with extensive experience in your industry can provide insights and solutions tailored to your specific needs.
- Quality Assurance: Look for manufacturers that adhere to high-quality standards and have robust quality control processes in place.
- Capacity and Flexibility: Ensure that the partner can accommodate your production volume while being flexible enough to adapt to changes in demand.
- Technology: Invest in a partner who embraces the latest technologies to maximize efficiency and minimize costs.
- Communication: Effective communication and transparency in operations lead to a smoother workflow and better outcomes.
Conclusion: The Future of Injection Moulding Manufacturing
As industries continue to evolve, the role of injection moulding manufacturing becomes increasingly significant. With a commitment to innovation, efficiency, and precision, businesses can harness the power of this manufacturing method to stay competitive in the market. From automotive parts to consumer products, the possibilities are virtually limitless.
In keeping with the principles of sustainability, the future of this industry also lies in embracing eco-friendly materials and processes. As a leading player in the field, DeepMould.net positions itself as a key partner in guiding businesses through the complexities of metal fabrication and injection moulding manufacturing.
By understanding the nuances of injection moulding and leveraging cutting-edge technology, companies can ensure that their production processes are optimized for success. As we look to the future, the importance of strategic partnerships in injection moulding will undoubtedly shape the next generation of products that define our lives.