The Ultimate Guide to Plastic Mold Making
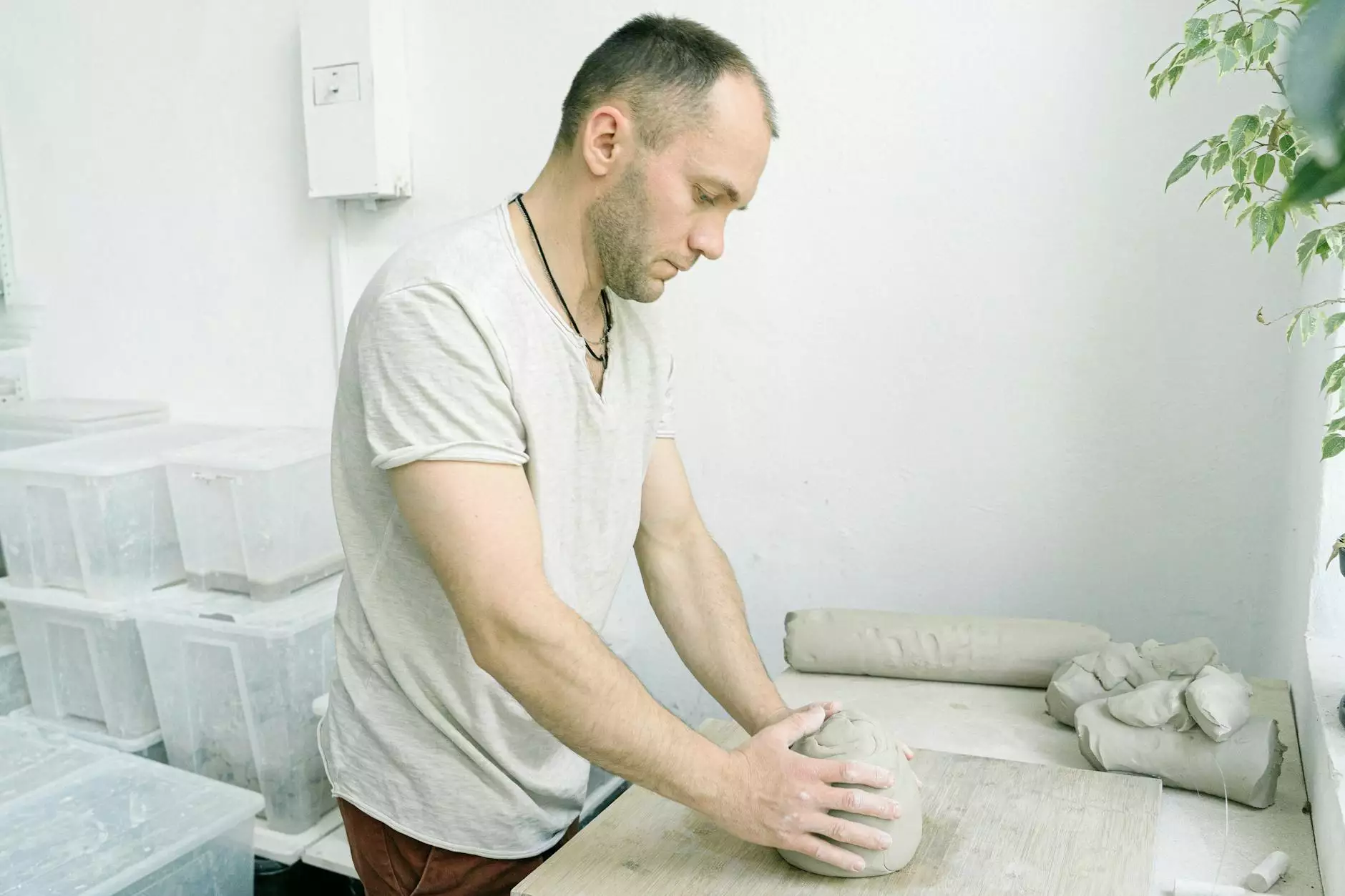
In today’s fast-paced manufacturing environment, becoming a successful plastic mold maker requires a blend of technical expertise, innovation, and efficiency. This article explores the nuances of plastic mold making, providing a detailed overview of the process and its importance in various industries.
What is a Plastic Mold Maker?
A plastic mold maker is a skilled professional or company that specializes in designing and fabricating molds used to produce plastic parts. These molds are essential in the injection molding process, where molten plastic is injected into the mold cavity to create a solid plastic item. The role of a plastic mold maker is crucial in ensuring high-quality production and meeting market demands.
Key Responsibilities of a Plastic Mold Maker
The responsibilities of a plastic mold maker can be quite extensive. Below are some of the core duties associated with this profession:
- Designing Molds: Utilizing CAD (Computer-Aided Design) software to create precise mold designs that meet industry specifications.
- Fabricating Molds: Employing various machining techniques such as milling, turning, and EDM (Electrical Discharge Machining) to produce high-quality molds.
- Testing and Quality Assurance: Conducting tests on molds to ensure they meet specifications. This includes assessing the mold’s ability to produce consistently accurate parts.
- Maintenance and Repair: Performing routine maintenance on molds to prevent wear and tear, and undertaking repairs as necessary to extend mold life.
- Collaboration with Engineers: Working closely with product engineers to innovate and refine mold designs for improved efficiency and functionality.
The Importance of Plastic Molds in Manufacturing
Plastic molds play a pivotal role in various sectors, including automotive, consumer goods, electronics, and medical devices. Here are a few reasons why plastic molds are indispensable:
- Cost Efficiency: Once a mold is designed and produced, it can be used for mass production, significantly reducing the cost of manufacturing individual plastic parts.
- Design Flexibility: Molds can be designed to create complex shapes and intricate details, opening up possibilities for innovative products.
- Consistency and Quality: Using molds ensures uniformity in product quality, as each item produced is identical to the last.
- Speed of Production: The injection molding process is quick, allowing for high-volume outputs in a fraction of the time required for other manufacturing methods.
The Plastic Injection Molding Process
Understanding the plastic injection molding process is essential for any plastic mold maker or manufacturer. The process involves several systematic steps:
1. Material Selection
Choosing the right type of plastic resin is critical for achieving desired characteristics in the final product. Factors like color, strength, flexibility, and chemical resistance play significant roles in this decision.
2. Mold Design
After the material is selected, the next step is to design the mold. This includes calculations for gate placement, cooling systems, and venting to ensure efficient manufacturing.
3. Mold Fabrication
Using high-precision machines, the mold is manufactured according to the design specifications, often requiring intricate machining work to achieve the desired outcome.
4. Injection Process
The plastic resin is fed into an injection molding machine, where it is melted and injected into the mold under high pressure. Once the material fills the mold, it cools and solidifies into the final product.
5. Ejection and Finishing
After cooling, the mold opens, and the finished product is ejected. Additional finishing processes may be required, such as trimming, painting, or assembly, depending on the product's specifications.
Choosing the Right Plastic Mold Maker
Selecting the right plastic mold maker is vital for the success of your project. Here are some tips on how to make the right choice:
- Experience: Look for a mold maker with extensive experience in your industry. A seasoned professional will likely understand the unique challenges and requirements of your project.
- Portfolio: Review their previous work to assess the quality and variety of molds they have produced. A diverse portfolio is often an indicator of innovation and capability.
- Technology: Ensure that they utilize up-to-date technologies and techniques. Modern machinery and software can lead to more accurate and efficient mold production.
- Customer Service: A responsive and communicative mold maker will facilitate a smoother project transition. Effective collaboration is key to implementing necessary changes and improvements throughout the process.
- Reviews and Testimonials: Research feedback from previous clients to gauge reliability and quality of service. Positive reviews can reassure you of the company’s commitment to excellence.
The Future of Plastic Mold Making
As technology continues to evolve, the field of plastic mold making is also transforming. Innovations such as additive manufacturing, advanced materials, and better software tools are shaping the future landscape of this industry. Key trends include:
- 3D Printing: This technology is increasingly being integrated into mold making, allowing rapid prototyping and design modifications without extensive downtime.
- Smart Manufacturing: Incorporating IoT and automation in production processes can enhance efficiency and reduce human error.
- Sustainability: There is a growing demand for sustainable practices, including the use of recyclable materials and energy-efficient production methods.
Conclusion
The role of a plastic mold maker is crucial in ensuring high-quality production and innovation across various sectors. By understanding the intricacies of the mold-making process and staying updated with industry advancements, mold makers can offer exceptional value to their clients. For companies seeking reliable and experienced solutions, partnering with the right mold maker can lead to significant advantages in terms of efficiency, cost savings, and product quality. Explore more about our services at hanking-mould.com to see how we can assist in your plastic injection mold manufacturing needs.